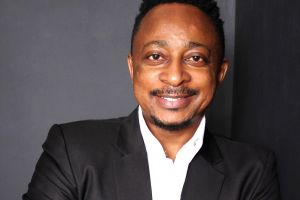
Motor industry reaches three-year wage agreement
The Retail Motor Industry Organisation (RMI) has announced the completion of the wage negotiations for 2025.
- Industry News
- 26 August 2025
A completely new high-tech body shop has been constructed at the Ford Motor Company of Southern Africa’s plant as part of the company’s R15.8 billion investment in its assembly plant operations in Silverton, Pretoria.
Ockert Berry, the Vice President Operations for Ford South Africa, says building a new body shop was essential for the Silverton assembly plant to achieve its highest installed capacity to date of 200 000 vehicles a year.
“This necessitated a much higher level of automation to reach our production targets while also introducing the latest quality control systems and technologies that are essential for delivering consistent, world-class quality vehicles for our local and export customers,” he says.
The new 44 000 m2 body shop features the highest-ever levels of automation and quality control for the facility, which will be producing the next-generation Ford Ranger for domestic sales and export to more than 100 markets globally.
The plant manufactures a wide variety of configurations of the Ford Ranger, including single cab, supercab and double cab, apart from left-hand drive and right-hand drive derivatives.
The new body shop and its supporting warehouse are located adjacent to the recently completed stamping plant, which will provide a seamless flow of stamped panels to the line where the body and load compartment of the Ranger pick-up are assembled and welded.
The highly automated production line is designed around 493 robots that transform the many stamped body panels, including the underbody, floor, roof, body sides, cab framing and load box, into a complete Ranger body ready for transfer to the paint shop.
The robotic welding guarantees the highest level of consistency by employing the latest 100% adaptive controllers with servo guns to deliver spatter-free body welds.
Adheer Thakurpersad, the area manager for the body shop, says designing and building the new body shop from the ground up have allowed Ford South Africa to integrate IIOT (Industrial Internet of Things) into the manufacturing areas.
“This gives our production teams access to in-depth and always up-to-date analysed data trends, which allow them to make concise decisions to consistently improve productivity and quality,” he says.
Significant investment has been made in quality control technologies, including two inline Perceptron measuring systems that measure and record every vehicle manufactured in the body shop plus the respective Geometric pallets that they are assembled on.
Vision systems attached to sealer application robots provide further error-proofing in support of Ford’s commitment to setting an even higher standard for quality, reliability and durability with the next-generation Ranger.
The handling of the vehicle body during construction has also been automated on the line to totally eliminate the need to move parts manually, which could result in damage.
Thakurpersad added that to assess the weld quality, they conduct non-destructive testing and ultrasonic verifications and have a fully equipped destructive teardown facility to test the integrity of the weld spots.
“It’s not just the high-tech equipment and systems that contribute to quality and efficiency, as the production team continues to play a critical role, with the body shop team comprising 38 salaried and 500 hourly paid employees.
“Being in a highly automated environment, ongoing skills development is a priority. Therefore we have plans to install an advanced skills development facility in the body construction area, which will enable employees to continue developing their skills in automation and problem-solving,” he says.
The Retail Motor Industry Organisation (RMI) has announced the completion of the wage negotiations for 2025.
This weekend all roads lead to the Kyalami Grand Prix Circuit for the annual Festival of Motoring.
Chery has made history in South Africa by successfully conducting Africa’s first real-world dual-vehicle collision test.